Transforming Manufacturing with **Insert Molding Solutions**
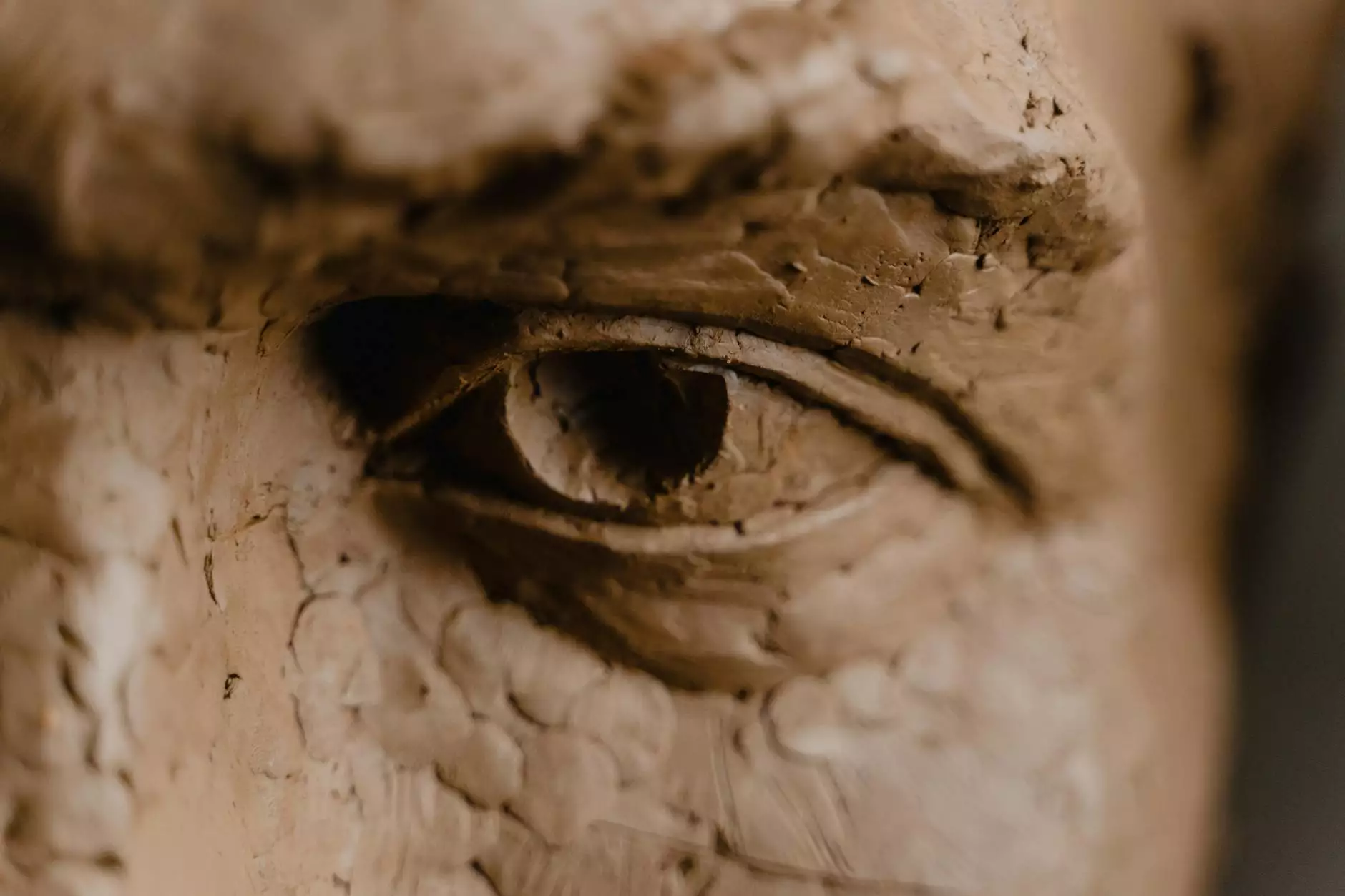
In the rapidly evolving world of manufacturing, the quest for efficiency, quality, and innovation drives companies to seek advanced techniques that can streamline their processes. One such technique that has garnered significant attention in recent years is insert molding solutions. This versatile method not only enhances the durability and functionality of products but also plays a crucial role in reducing production costs and time.
What is Insert Molding?
Insert molding is a specialized injection molding process where pre-formed components are placed into a mold cavity prior to the injection of molten plastic. This method allows for the creation of complex plastic parts that incorporate metal or other materials, resulting in a stronger and more reliable product. The process can be broken down into a few key steps:
- Preparation: Pre-formed inserts are manufactured or sourced to meet the design specifications.
- Molding: Inserts are placed in a mold, followed by the injection of plastic.
- Cooling: The assembly is allowed to cool and solidify.
- Finishing: The molded part is removed from the mold, ready for further processing if necessary.
Advantages of Using Insert Molding Solutions
The use of insert molding solutions provides several compelling benefits that can greatly impact the manufacturing process:
1. Enhanced Product Strength
By integrating stronger inserts, manufacturers can create components that withstand greater stresses, which is particularly important in industries such as automotive, aerospace, and electronics. The combination of materials allows for performance that is often superior to that of standalone molded parts.
2. Cost Efficiency
Though the initial setup for insert molding might be slightly more complex, the overall savings in production costs can be significant. The reduction in the number of assembly steps required leads to less labor and shorter production cycles, ultimately driving down costs.
3. Design Flexibility
Insert molding opens a world of design possibilities. Engineers can experiment with various materials and geometries, allowing for tailored solutions that meet specific needs. For example, combining plastic with metal inserts is highly effective for electronic housings that require EMI shielding.
4. Improved Aesthetics
The precision of insert molding often results in high-quality finishes and designs that are visually appealing. This is particularly important in consumer products, where appearance can significantly influence purchasing decisions.
5. Reduced Waste
Through insert molding, material waste is minimized. This not only contributes to environmental sustainability but also maximizes the use of raw materials, resulting in more cost-effective production practices.
Applications of Insert Molding Solutions
Insert molding solutions find their applications in various industries, each benefiting from the unique advantages of this manufacturing technique:
1. Automotive Industry
The automotive industry is a prime candidate for insert molding due to its requirement for lightweight, durable components. Parts such as connectors, housings, and brackets benefit from the strength provided by metal inserts.
2. Electronics
In the electronics sector, insert molding is utilized to produce components like circuit boards and housings. The technique allows for efficient production of parts that not only hold up against wear but also ensure prolonged functionality.
3. Medical Devices
Medical devices require high precision and reliability. Insert molding helps ensure that these critical components meet stringent regulatory requirements while maintaining performance and sterility.
4. Consumer Goods
Everyday items, from tools to packaging, can benefit from the enhanced durability and cost savings provided by insert molding solutions. The ability to create multi-material products opens up design opportunities for manufacturers.
Choosing the Right Insert Molding Partner
Finding the right partner for your insert molding solutions is crucial for product success. Consider the following when choosing a manufacturer:
- Experience: Look for a company with a proven track record in the industry.
- Technology: Ensure they use advanced technologies that enhance quality and efficiency.
- Customization: Your partner should be capable of offering tailored solutions to fit your specific needs.
- Quality Assurance: Focus on companies that prioritize quality control at every stage of production.
FAQs About Insert Molding Solutions
What materials are commonly used in insert molding?
Common materials include a wide range of thermoplastics and thermosetting plastics, along with metals like aluminum and steel which are used for the inserts.
How does insert molding compare to traditional plastics molding?
Insert molding integrates additional materials into the manufacturing process, while traditional molding typically focuses solely on plastic. This results in parts with enhanced capabilities in terms of strength, durability, and functionality.
Can any shape be molded using insert molding?
While insert molding is versatile, the design must be feasible for the mold-making process. Therefore, complex designs may require careful consideration during the engineering phase.
What is the typical lead time for insert molding projects?
Lead times vary based on complexity and volume, but generally, around 6 to 12 weeks is standard after initial designs are approved and molds are created.
Hanking Mould: Your Partner in Insert Molding Solutions
At Hanking Mould, we specialize in providing state-of-the-art insert molding solutions tailored to your business's unique needs. As a leading plastic mold maker and plastic injection mold manufacturer, we are committed to quality and customer satisfaction. Our team of experts utilizes the latest technology and methodologies to ensure that your products not only meet but exceed your expectations.
Our comprehensive services include:
- Custom Mold Design: Personalized designs to suit your product needs.
- Advanced Manufacturing: Utilizing cutting-edge technology for precise results.
- Quality Assurance: Rigorous testing and quality checks throughout the production process.
- Rapid Prototyping: Quickly designing and testing prototypes to ensure optimal functionality.
Conclusion: The Future of Manufacturing with Insert Molding Solutions
The introduction of insert molding solutions has revolutionized manufacturing across various industries, providing companies with unmatched advantages in terms of product durability, cost savings, and design flexibility. As industries continue to evolve towards more sustainable and efficient practices, insert molding stands out as a robust solution that aligns with these goals.
Partnering with experts like Hanking Mould can help your business achieve its objectives while maintaining high standards of quality and efficiency. Transitioning to insert molding could very well position your company at the forefront of innovation in your industry.