Understanding the Role of Injection Plastic Mold Manufacturers
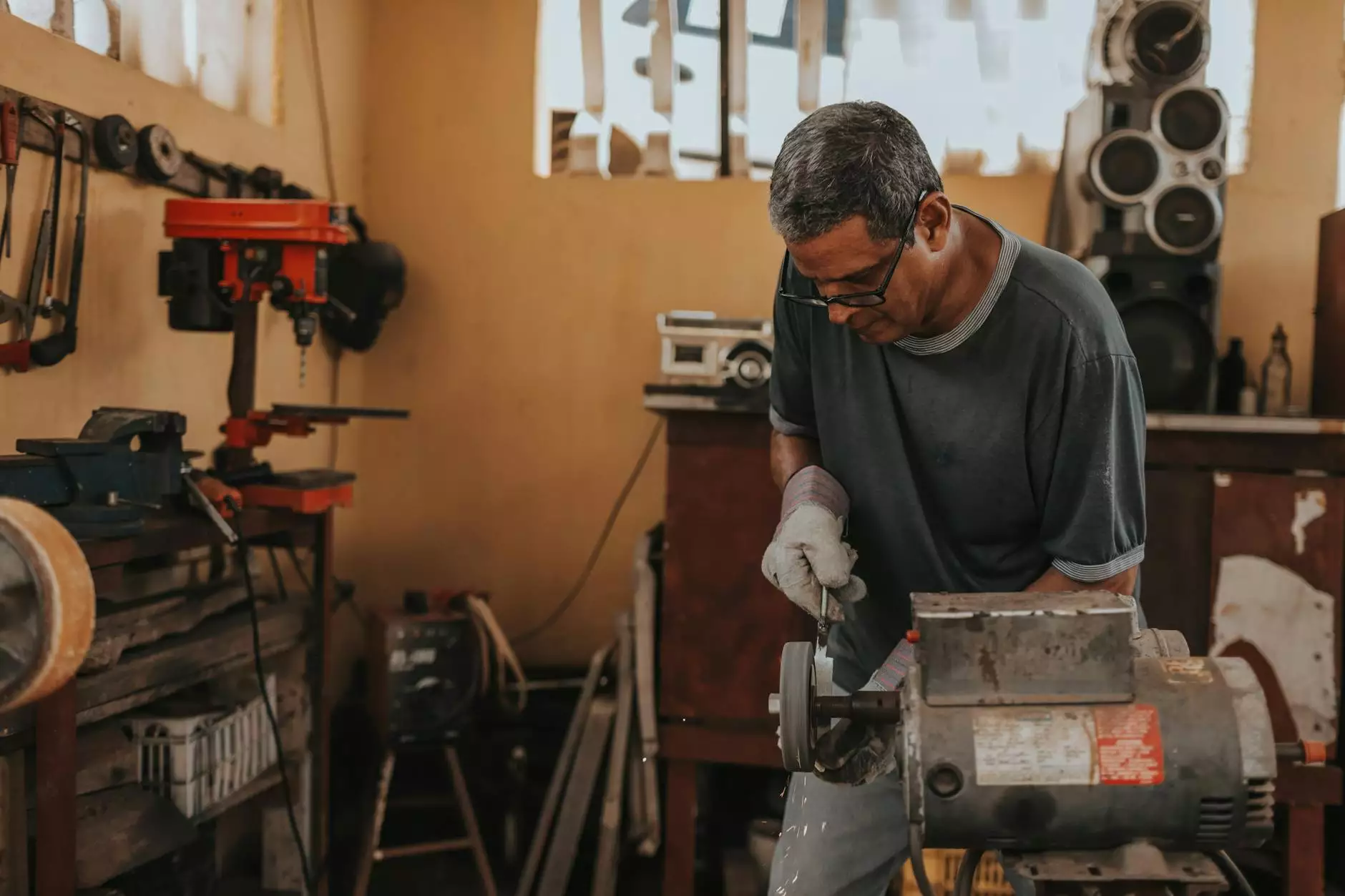
The landscape of modern manufacturing is continuously evolving, and nowhere is this more evident than in the realm of injection plastic mold manufacturers. These companies specialize in designing and producing molds that are critical in creating plastic components used across various industries. In this comprehensive guide, we will explore the intricacies of the injection molding process, the significance of choosing the right manufacturer, and how businesses can harness this technology for their production needs.
What is Injection Molding?
Injection molding is a manufacturing process for producing parts by injecting molten material into a mold. It is one of the most common methods used for creating plastic products due to its efficiency and ability to produce complex shapes. The process starts with melting plastic pellets and injecting the molten material into a pre-designed mold. Upon cooling and solidifying, the mold is removed, resulting in a finished product ready for further processing or use.
The Importance of Injection Plastic Mold Manufacturers
Injection plastic mold manufacturers play a pivotal role in ensuring that production lines are efficient and that the final products meet the standards required by various industries. Their expertise lies not only in creating the molds but also in understanding the specific needs of different markets.
- Customization: Each industry has unique requirements. Manufacturers can tailor molds to fit precise specifications, ensuring that the final product meets exacting standards.
- Quality Control: Established manufacturers possess quality assurance protocols that ensure every mold and the resulting product are made to high standards.
- Efficiency: With their expert knowledge, manufacturers optimize the injection process, reducing waste and lowering production costs.
The Process of Injection Molding
The injection molding process consists of several critical stages, each contributing to the efficiency and accuracy of the manufacturing. Here’s a detailed breakdown:
1. Material Selection
The first step involves selecting the appropriate plastic material based on the application. Common materials include:
- ABS (Acrylonitrile Butadiene Styrene)
- PP (Polypropylene)
- PS (Polystyrene)
- PE (Polyethylene)
- PVC (Polyvinyl Chloride)
2. Mold Design
The design of the mold is crucial. Manufacturers utilize advanced CAD software to create a 3D model that outlines every detail and specification required for production.
3. Mold Fabrication
Once the design is finalized, the mold is fabricated using high-quality materials. This stage often requires precision machining techniques to ensure that fits and tolerances are met.
4. Injection Molding
The molten plastic is injected into the mold under high pressure. The temperature and timing of injection are finely controlled to ensure the material fills the mold completely.
5. Cooling and Ejection
After the plastic has been injected into the mold, it is allowed to cool and solidify. Once at the appropriate temperature, the mold opens, and the finished product is ejected.
Factors to Consider When Choosing Injection Plastic Mold Manufacturers
Choosing the right injection plastic mold manufacturers can significantly impact the quality and efficiency of your production. Here are several key factors to evaluate:
- Experience: Look for manufacturers with a proven track record and extensive experience in your specific industry.
- Technology: Ensure the manufacturer employs the latest technologies in mold design and production. Advanced machinery leads to better precision and faster turnaround times.
- Customer Support: A reliable manufacturer offers ongoing support, from the initial consultation through to after-sale services.
- Cost Effectiveness: Evaluate quotes but do not compromise on quality. The cheapest option may not always be the best for your business needs.
Applications of Injection Molding
The versatility of injection molding enables its use across a plethora of industries, including:
1. Automotive Industry
Injection molding is extensively used to manufacture parts like dashboard components, bumpers, and other interior/exterior elements essential for vehicle functionality and aesthetics.
2. Consumer Electronics
From mobile phone casings to remote control housings, injection molded plastic parts form the backbone of modern electronics, offering durability and lightweight benefits.
3. Medical Devices
Injection molding is vital for producing medical-grade components that comply with strict regulatory standards, ensuring safety and efficacy in health care applications.
4. Packaging
Many packaging solutions, such as containers, closures, and dispensers, utilize injection molding to create lightweight and versatile designs.
Environmental Considerations in Injection Molding
With growing environmental concerns, injection plastic mold manufacturers are increasingly focusing on sustainability. Considerations include:
- Material Selection: Using recycled plastics or biodegradable materials helps reduce the environmental impact.
- Energy Efficiency: Modern injection molding machines are designed to consume less energy, minimizing the carbon footprint of production.
- Waste Reduction: Manufacturers are implementing processes to recycle scrap plastic directly back into the production cycle.
Conclusion
The role of injection plastic mold manufacturers is crucial for businesses looking to innovate and produce high-quality plastic parts. From understanding the injection molding process to evaluating manufacturers, it is paramount to engage with experts who can elevate your production capabilities. By selecting the right partner, businesses can ensure efficiency, cost-effectiveness, and sustainability in their manufacturing processes.
To learn more about our services at DeepMould and how we can assist you with all your injection molding needs, feel free to contact us today!